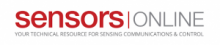
The automotive industry is adopting self-driving cars as the next major evolutionary step in vehicular technology. However, improvements need to be made to data buses inside the car to support the additional data needed for a car to operate autonomously. Ethernet and the Mobile Industry Processor Interface (MIPI) are replacing previous network technologies, allowing for the next generation of autonomous vehicles through faster data rates and lower latency.
Introduction
For the better part of the last century, automotive makers have been creating new and innovative technologies with the goal of designing fully autonomous vehicles. The concept of a highly autonomous and self-driven vehicle can be dated back to at least the 1950’s with the idea being glorified throughout pop culture in the following decades, such as comic books, TV, and film. However, only in the last 20 years have the technological improvements in the car advanced enough to support such applications. Vehicle to Vehicle (V2V) and Vehicle to Infrastructure (V2I) wireless communication protocols have revolutionized the future of autonomous vehicles, but a fast, reliable, and robust wired backbone is still needed to meet the bandwidth needs of systems and sensors within the car.
For decades each Automotive OEM used proprietary technologies to enable new features in their vehicles, but eventually some technology standards (CAN, Flexray) were developed for the specific needs of the automotive industry and adopted by OEMs. However, the bandwidth capabilities of these networks quickly became inadequate for the growing number of sensors needed to make the self-driving car a reality.
About 10 years ago, the automotive industry looked to other network technologies and architectures to overcome these bandwidth limitations and recognized Ethernet as a potentially viable option. Additionally, MIPI has recently gained the attention of automotive OEMs as well because the solutions are mature, relatively simple to use, and help reduce the number of wires needed to connect components.
Brief History of Automotive Ethernet
Ethernet was first considered for in-vehicle applications around 2008, but it never quite took off during that time. For starts, 100-Mbps twisted-pair Ethernet (100BASE-TX - Fast Ethernet) was installed and used mostly for diagnostic applications and servicing electronic control units (ECUs). It was not used as a data bus during vehicle operation because of poor EMI performance. Additionally, ECU data polling and firmware updates required the transfer of large sets of data, leading to long vehicle service times.
Lastly, Ethernet was not designed to be a lossless network, and Automotive applications require guaranteed bandwidth and latency for safety reasons. However, it was during this time that the Automotive industry would start to recognize the key benefits of Ethernet: reduced cost, proven interoperability, and network ubiquity.
“Automotive Ethernet” - Improvements to Previous Ethernet PHYs
After recognizing the benefits of Ethernet over other comparable technologies, the automotive industry kept a watchful eye on developments within IEEE 802. A few years later, the IEEE 802.1 Working Group started developing Time Sensitive Network (TSN) specifications that would remedy the guaranteed bandwidth and latency concerns. Since the TSN specifications were creating a way to solve the latency issue, the need for an automotive-specific Ethernet PHY could be discussed.
In 2012, ambassadors of the automotive industry attended the IEEE 802.3 Working Group meeting to build consensus to create an Ethernet PHY project specific to the automotive industry’s needs. In the six years since that decisive meeting, there have been three IEEE 802.3 projects specific to the automotive market including 100 Mbps and 1000 Mbps PHY definitions. Both PHYs are specified to operate over 15 meters of a single unshielded twisted-pair cable, half as much cabling as 100BASE-TX and one quarter the cabling needed for 1000BASE-T, leading to weight and cost reductions when installing the vehicle cable harness.
They also have improved EMC requirements to accommodate the harsh RF environment of a motor vehicle. These characteristics combined with the IEEE 802.1 TSN protocols, create a cost competitive solution that is reliable, high bandwidth, and multi-vendor interoperable, allowing for greater network flexibility and scaling, while lowering complexity and cost.